Most Common Mistakes In Brick Masonry and How to Avoid Them

Table of Contents
Brick masonry is one of the most fundamental elements of construction. It has been used for centuries to build everything from humble homes to towering structures. However, the quality and durability of brick masonry largely depend on the techniques employed during its execution. Even minor mistakes can compromise the structural integrity and longevity of a project.
In this blog, we will explore the most common mistakes made during brick masonry and provide practical solutions to avoid them. Whether you’re a construction professional or someone looking to better understand the process, this guide will equip you with the knowledge to achieve impeccable results.
Essential Principles of Brick Masonry
To understand and avoid mistakes, it’s crucial to grasp the foundational principles of brick masonry.
- Understanding Mortar Mixtures
Mortar acts as the binding agent in brick masonry. Using incorrect proportions of cement, sand, and water often leads to weak joints or cracks. Always follow the recommended mix ratios for specific applications and ensure the mortar is neither too dry nor overly wet.
- Selecting Quality Bricks
Not all bricks are created equal. Using low-quality bricks with inconsistent sizes or poor compressive strength can weaken the structure. Always inspect bricks for uniformity, durability, and compliance with industry standards before use.
- Importance of Workmanship
Even with the best materials, poor workmanship can ruin masonry. This includes uneven brick placement, improper leveling, and rushed execution. Skilled professionals who pay attention to detail ensure a strong, aesthetically pleasing result.
Most Common Mistakes In Brick Masonry
1. Irregularly shaped bricks
Irregularly shaped bricks can lead to inconsistent bonding and create gaps in the structure, which compromises the overall strength of the masonry. Such bricks can be difficult to lay correctly and may require excessive mortar, which can weaken the wall. To avoid these issues, it’s essential to use well-shaped, uniform bricks that fit together seamlessly.
Additionally, the quality of the brick is vital to the integrity of the structure. Poor-quality bricks that are irregular in shape might also lack the necessary compressive strength to withstand load-bearing stress.
Best Practices:
- Ensure that bricks are manufactured according to proper standards, which guarantee uniformity in size and shape.
- Conduct quality checks on bricks before use to ensure they meet required specifications.
2. Use of dry bricks
Using dry bricks, particularly in hot weather, can result in poor adhesion between the mortar and brick. Mortar requires sufficient hydration to set and bond effectively. When dry bricks are used, they absorb moisture from the mortar, causing it to dry too quickly and weakening the bond. This can lead to cracks and a decrease in the overall durability of the structure. We are very careful of these minute details at the time of constructing high-rise buildings at Dhinwa construction. It ensures that the structures we build are reliable in the long term.
Best Practices:
- Wet the bricks slightly before use, especially in hot and dry climates, to prevent them from drawing moisture out of the mortar.
- Avoid using bricks that have been exposed to rain or moisture, as they can cause efflorescence and weaken the wall’s longevity.
3. Mistakes in bed joints
The bed joint refers to the horizontal layer of mortar between each row of bricks. Errors in creating bed joints, such as inconsistent mortar thickness, improper mixing, or failure to fully fill the joint, can lead to weak spots in the wall. These weaknesses may cause the structure to settle unevenly or lead to cracks. It is crucial that each bed joint is properly formed to ensure even load distribution across the wall.
Best Practices:
- Mortar should be applied evenly to each bed joint, ensuring there is no excessive buildup or gaps.
- Check the consistency of the mortar to ensure it is neither too thick nor too thin for the required bonding.
4. Skipping Proper Curing
Curing is an essential process for ensuring the strength and durability of brick walls. When curing is neglected, the mortar doesn’t set properly, and cracks may form. Proper curing allows the hydration of cementitious materials in the mortar, which significantly enhances its compressive strength. In hot and dry weather conditions, this is even more critical as the moisture content can evaporate quickly.
Best Practices:
- Curing should begin immediately after laying the bricks and continue for at least 7 days for optimal mortar strength.
- Keep the brick and mortar moist, especially during the initial stages, using water spraying or wet coverings.
5. Using Inconsistent Mortar Thickness
Inconsistent mortar thickness can result in uneven load distribution across the wall, leading to potential structural failure. Thin mortar layers may not bond the bricks securely, while thick mortar layers can result in excessive shrinkage and cracking. The ideal thickness for bed joints is typically between 10–12 mm, which provides enough space for the mortar to bond while maintaining the brickwork’s stability.
Best Practices:
- Always measure and control mortar thickness to maintain uniformity.
- Use mortar boards or gauges to achieve consistent joint thickness throughout the project.
6. Ignoring Vertical Alignment
Vertical alignment is crucial in masonry construction as it ensures the stability and straightness of the walls. Poor alignment, such as leaning or bowing walls, can compromise the load-bearing capacity and aesthetic appeal. Even slight misalignments can worsen over time due to external forces like wind and load stress, causing long-term structural issues.
Best Practices:
- Regularly use a plumb line or spirit level to check the vertical alignment of your walls during construction.
- Always adjust the position of bricks as you work to ensure they remain straight and true.
7. Overlooking Expansion Joints
Thermal expansion and contraction, especially in large masonry structures, can cause stress on the walls, leading to cracks. Expansion joints are essential to accommodate this movement and prevent damage. If these joints are not planned and placed properly, the wall could become prone to structural cracks as the materials expand and contract with temperature fluctuations.
Best Practices:
- Place expansion joints at appropriate intervals, typically every 10 to 15 meters for large walls, and in areas with varying temperature conditions.
- Ensure expansion joints are filled with compressible material to allow for movement while preventing debris from entering the joint.
8. Neglecting Bond Patterns
The brick bond pattern determines the interlocking and strength of the wall. Incorrect bond patterns can lead to weak points where bricks don’t effectively interlock, compromising the overall structural integrity. For example, a running bond may be simpler to construct but does not provide as much strength as an English bond, which alternates between headers and stretchers to create a more interlocked structure.
Best Practices:
- Always follow established bond patterns such as English bond, Flemish bond, or stretcher bond, depending on the structural needs.
- Choose the appropriate bond pattern based on the type of structure and the load-bearing requirements.
Preparation and Planning
1. Site Analysis and Material Handling
Analyze the site’s conditions and store materials properly to avoid damage. Bricks should be kept on a dry, elevated surface to prevent moisture absorption.
Having worked on numerous high-rise construction projects, one thing we can confidently say is that if the contractor you hired isn’t attentive to site analysis and material handling then the entire procdure of construction is going to suffer.
2. Design Considerations and Dimensions
Ensure designs are practical and consider brick dimensions to avoid excessive cutting and wastage. Always double-check measurements before starting.
Laying Techniques for Stability
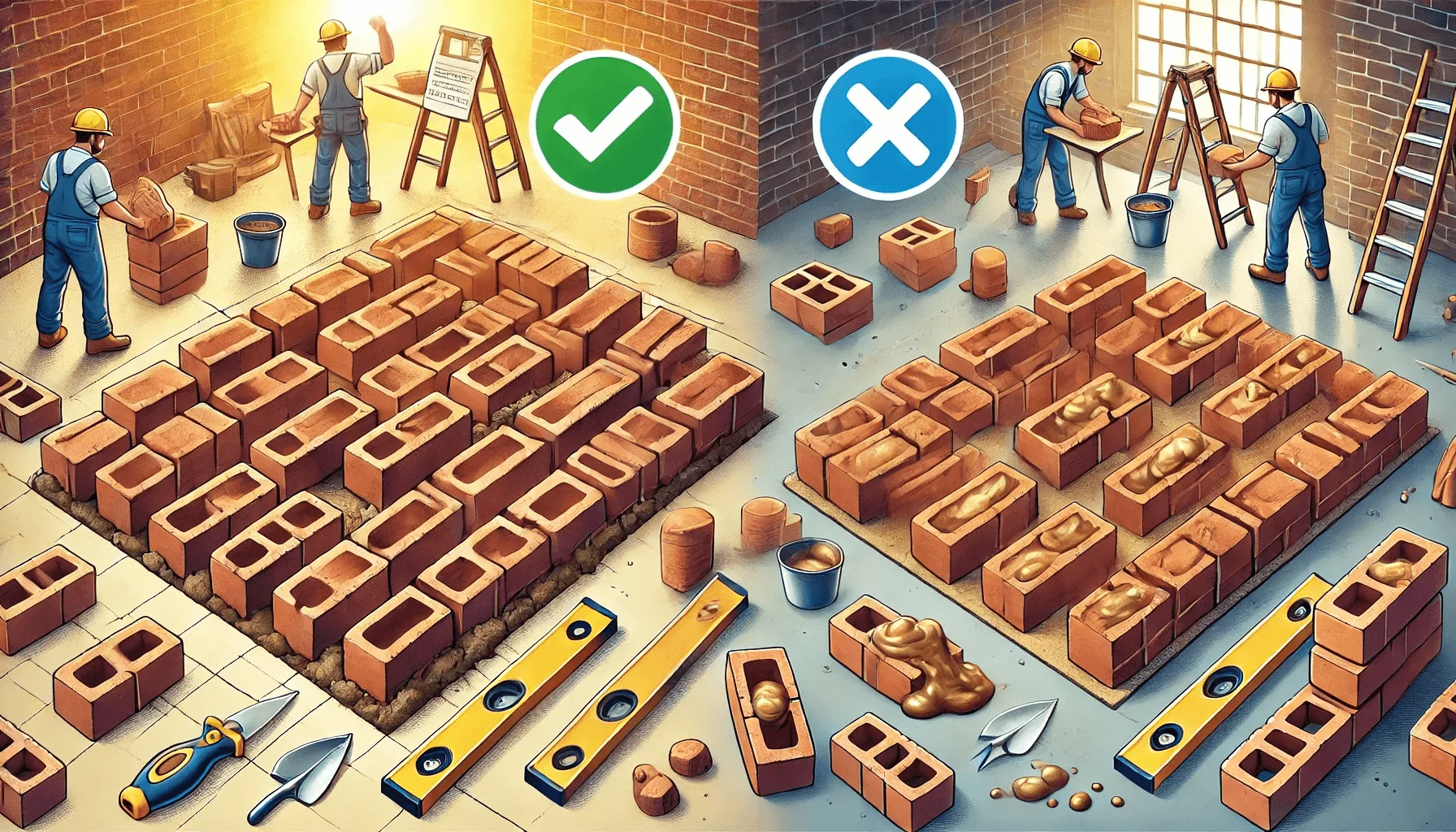
1. Foundational Layer Accuracy
The foundational layer is the most critical as it serves as the base for the entire structure.
- Precision in Measurement: Begin by marking the layout using accurate measurements to ensure the bricks are placed exactly where they need to be.
- Tools for Perfection: Use tools such as a spirit level, trowel, and string line to maintain evenness.
- Material Preparation: Ensure the mortar consistency is neither too wet nor too dry, as this can affect the placement of bricks and lead to gaps.
- Inspection: Regularly inspect the foundation during and after laying the first layer to address errors immediately.
2. Brick Bond Selection
Selecting the right brick bond enhances the stability and load distribution of the wall.
- Common Bond Types: Understand and choose between stretcher bond, header bond, English bond, or Flemish bond, depending on the project’s strength and aesthetic requirements.
- Structural Integrity: Proper bonding patterns reduce the chances of weak points and improve resistance to external pressures.
- Cost-Effectiveness: Some bonds require fewer materials while maintaining strength; analyze the design to balance cost and functionality.
3. Verticality and Straightness
Maintaining vertical alignment is essential for structural safety and aesthetic appeal.
- Continuous Monitoring: Use a plumb line, spirit level, and laser level at regular intervals during the construction process.
- Avoid Deviations: Even slight deviations in alignment can compromise the wall’s strength, leading to safety issues over time.
- Anchoring Techniques: For high-rise constructions or windy areas, incorporate anchoring mechanisms to ensure walls remain vertical under load.
- Finishing Touch: Before moving to the next layer, verify the straightness and alignment to ensure a seamless transition.
Being in the construction industry for years, we would suggest everyone to not take these instructions lightly as long as the goal is to build a building that lasts.
Common Errors in Mortar Application
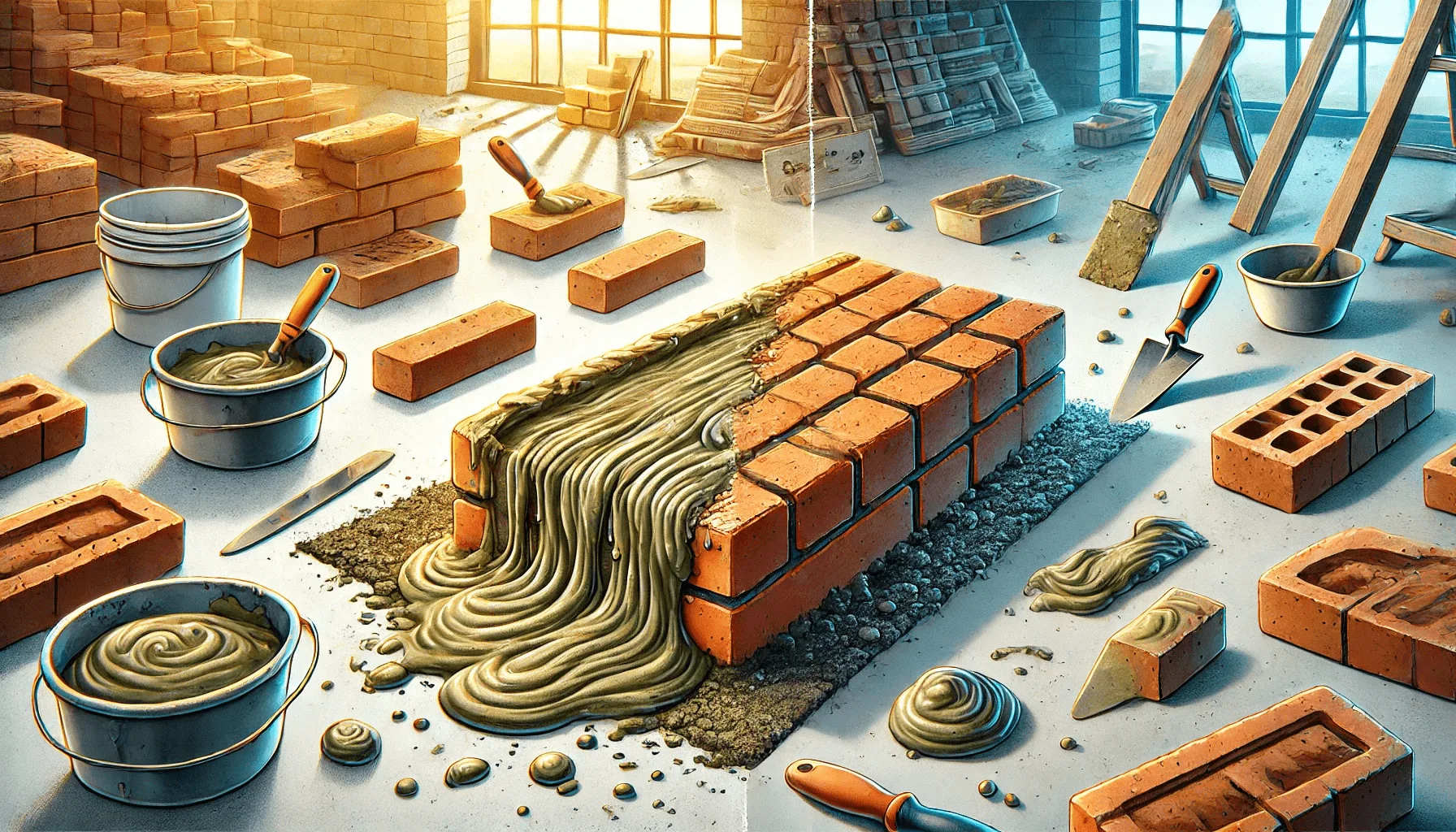
1. Incorrect Mortar Consistency
Mortar that is too thick or runny leads to poor adhesion. Mix mortar until it has a workable consistency.
2. Inadequate Mortar Curing
Mortar needs proper curing to gain full strength. Protect fresh masonry from direct sunlight or heavy rains during curing.
Structural Integrity Challenges

1. Weep Hole Implementation
Weep holes allow moisture to escape from walls. Skipping or improperly placing them can trap water, leading to long-term damage.
- Functionality: Weep holes allow trapped water within the cavity walls to drain, reducing the risk of mold, mildew, and material deterioration caused by prolonged dampness.
- Placement Guidelines: Position weep holes above flashing layers, at the base of cavity walls, and near windows or doors. They should be spaced every 1 to 1.2 meters horizontally to ensure adequate drainage.
- Material Selection: Use durable, corrosion-resistant materials like plastic weep hole covers to prevent clogging and ensure longevity.
- Common Errors: Blocking weep holes during construction with mortar or debris is a frequent oversight that nullifies their purpose.
- Maintenance Tips: Regularly inspect weep holes to confirm they are unobstructed and functional, especially in high-rainfall areas.
2. Control Joint Misplacement
Control joints prevent cracking in large walls. Misplacing them compromises wall flexibility.
Control joints are indispensable for managing wall expansion, contraction, and cracking due to temperature changes or shrinkage.
- Strategic Placement: Install control joints in long masonry walls at intervals of 20–30 feet, or as specified by design codes, to absorb movement and prevent stress buildup.
- Design Integration: Align control joints with wall features like doors, windows, or column edges to preserve structural and aesthetic continuity.
- Correct Installation: Cut joints to the appropriate depth, usually one-quarter to one-third of the wall thickness, and fill them with flexible sealants to accommodate movement without causing structural damage.
- Failure Risks: Poorly placed or missing control joints can lead to severe wall cracking, jeopardizing both safety and appearance.
- Regular Assessment: Periodic inspections help identify wear or sealant degradation, allowing timely repairs to maintain wall flexibility.
If you’re looking for experts in high-rise construction, contact us to learn more about our services.
3. Inadequate Reinforcement
Reinforcement ensures that walls can bear loads effectively and withstand external forces, especially in seismic zones.
- Seismic Resilience: Reinforce walls with steel bars, mesh, or grouted cores to enhance their ability to withstand earthquakes and other lateral forces.
- Proper Placement: Reinforcement bars should be placed at regular intervals, such as vertically every 24 inches and horizontally every 16 inches, or as per structural design requirements.
- Connection to Foundation: Anchor reinforcement into the foundation to form a cohesive structure that moves as a unit under stress.
- Compliance with Codes: Adhere to building codes that mandate specific reinforcement patterns, especially for high-risk areas like earthquake-prone regions.
- Inspection Practices: Before laying bricks or pouring concrete, ensure reinforcement is clean, properly aligned, and securely positioned to avoid weak points.
Weather and Climate Considerations
1. Adapting to Temperature and Humidity
Temperature extremes affect the curing process. Adjust mortar mix and curing techniques based on weather conditions.
2. Protecting Masonry During Inclement Weather
Cover walls with tarps or protective sheets during rain or harsh sunlight to prevent damage.
Finishing and Aesthetic Aspects
1. Pointing for Durability and Appeal
Proper pointing enhances both the appearance and durability of brickwork. Use appropriate tools to ensure clean, even joints.
2. Color Consistency and Matching
Inconsistent brick-and-mortar color disrupts the aesthetics of masonry. Use materials from the same batch and mix mortar thoroughly for uniformity.
Maintenance and Upkeep
1. Regular Inspection Routines
Inspect brick walls periodically for cracks, efflorescence, or other signs of wear. Early detection prevents major repairs.
2. Repair Techniques for Longevity
Use proper repair techniques like repointing or crack stitching to restore the wall’s strength and appearance.
Innovations in Brick Masonry
1. Modern Tools and Equipment
Technological advancements like bricklaying robots and laser levels enhance precision and efficiency in masonry.
2. Sustainable Practices
Eco-friendly practices, such as using fly ash bricks or recycled materials, reduce the environmental impact of masonry construction.
Conclusion
Brick masonry, while timeless, requires meticulous attention to detail to ensure durability and aesthetics. By understanding the common mistakes and employing the right techniques, you can avoid pitfalls and create structures that stand the test of time.
At Dhinwa Construction & Engineering, we prioritize quality and precision in every brick we lay. Our commitment to excellence ensures that our projects not only meet but exceed industry standards. Connect with us today to learn more about how we build structures designed to last for generations.